Sheet Metal Products
Sheet metal products are widely used across industries due to their durability, flexibility, and versatility in applications ranging from construction to automotive, aerospace, and consumer products. Here’s an in-depth guide on sheet metal products, their types, and fabrication processes.
- Common Sheet Metal Products
Enclosures and Cabinets:
Used for housing electrical components, equipment, or machinery (e.g., server racks, control panels, HVAC enclosures).
Made from materials like galvanized steel, aluminum, or stainless steel.
Automotive Body Panels:
Sheet metal is heavily used in manufacturing car hoods, doors, fenders, and other exterior body parts. These are typically made of steel or aluminum for strength and light weight.
Appliance Housings:
Washing machines, refrigerators, ovens, and other household appliances rely on durable sheet metal for outer casings.
Ductwork and Ventilation:
Sheet metal products like ducting, chimneys, and ventilation shafts are often fabricated using galvanized steel or aluminum for corrosion resistance.
Brackets and Mounts:
Small to medium-sized brackets used to secure structures, shelving, or machinery components.
Roofing and Cladding:
Metal roofing sheets, wall claddings, and facades are commonly produced from materials like corrugated steel, aluminum, or zinc-coated steel.
Furniture Components:
Office desks, storage units, and modular furniture frames are fabricated using sheet metal due to its strength and easy forming capability.
Signage:
Sheet metal is often used for making outdoor signage, advertisement panels, and lightboxes due to its ability to withstand harsh environments. - Materials Used in Sheet Metal Products
Stainless Steel:
Common in products where corrosion resistance is critical, such as kitchen appliances, medical equipment, and food processing machinery.
Aluminum:
Lightweight and resistant to corrosion, it’s frequently used in aerospace, automotive, and architectural applications.
Galvanized Steel:
Steel coated with zinc to prevent rust. It’s widely used in HVAC ducts, outdoor structures, and construction.
Copper and Brass:
These are used in decorative architectural elements, plumbing products, and electrical connectors due to their conductivity and appearance. - Fabrication Processes for Sheet Metal Products
Cutting:
Laser Cutting: High precision cutting for detailed shapes, suitable for prototypes or production runs.
Plasma Cutting: Used for cutting thicker sheets of metal quickly.
Water Jet Cutting: Ideal for cutting metals without affecting the material properties due to heat.
Shearing: A common method for straight-line cuts in large sheet metal panels.
Bending and Forming:
Press Braking: One of the most common methods of bending sheet metal into angular shapes such as brackets, enclosures, and frames.
Roll Forming: Continuous bending of long metal strips into complex profiles like channels or tubing.
Punching and Stamping:
Turret Punching: Used to cut or punch holes, slots, or shapes in the metal using a series of dies.
Stamping: High-volume production process where sheet metal is shaped or embossed using a stamping press. Common in automotive body panel production.
Welding:
MIG or TIG Welding is used to join sheet metal parts, especially when creating large enclosures or assemblies.
Spot Welding: A quick method to join thin sheet metal parts, often used in automotive manufacturing.
Forming:
Techniques like deep drawing are used to form metal sheets into cylindrical or box-like shapes for products like sinks or metal cans.
Surface Finishing:
Powder Coating or anodizing: Improves corrosion resistance and gives the product an aesthetic finish.
Electroplating: Adds a protective layer to improve durability and appearance. - Applications of Sheet Metal Products
Aerospace:
Sheet metal is used to create lightweight and strong parts like fuselage panels, wing components, and engine casings.
Automotive:
Body panels, frames, and interior components are fabricated using sheet metal.
Construction:
Structural elements such as beams, cladding, HVAC systems, and roofing are commonly made from sheet metal.
Consumer Products:
Everyday items like laptops, smartphone casings, and kitchen appliances use sheet metal for durability and sleek design. - Design Considerations for Sheet Metal Products
Material Thickness:
Choose the right gauge (thickness) based on the strength required. For example, thinner sheets (16-24 gauge) are ideal for ductwork, while thicker sheets (8-12 gauge) are used in structural components.
Bend Radius:
Properly calculated bend radii prevent cracking or deforming of the metal during bending. The material’s thickness will determine the minimum radius.
Tolerances:
Sheet metal tolerances vary depending on the fabrication method. Laser cutting offers tighter tolerances, while punching might have larger tolerances due to tool wear.
Fastening Methods:
Decide between welding, riveting, screws, or adhesives depending on the product’s function, durability, and aesthetic requirements.
Weight Considerations:
Lightweight metals like aluminum may be chosen for applications requiring easy handling, while heavier gauge steel might be needed for structural strength. - Challenges in Sheet Metal Fabrication
Springback:
After bending, sheet metal can spring back slightly due to its elastic properties. Adjust tooling to account for this in bending operations.
Material Wastage:
Efficient nesting (arranging parts on the sheet) can minimize scrap material and reduce costs.
Corrosion Resistance:
In applications exposed to the elements, appropriate surface treatments like galvanizing or powder coating are crucial for long-term performance. - Advanced Technologies in Sheet Metal Fabrication
Automation:
Automated machines such as CNC punch presses and robotic welding systems improve accuracy and reduce production time.
Laser Welding:
Enables high-speed welding with minimal distortion, especially in thin sheet metal assemblies.
3D Printing of Metal:
Some companies have started exploring additive manufacturing for thin metal components, allowing for more complex shapes. - Cost Factors for Sheet Metal Products
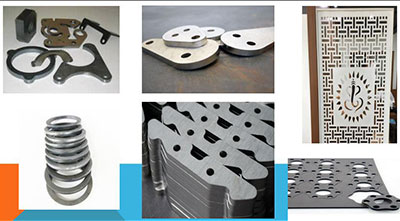
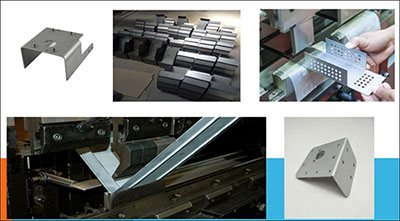
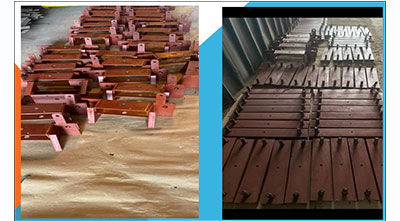
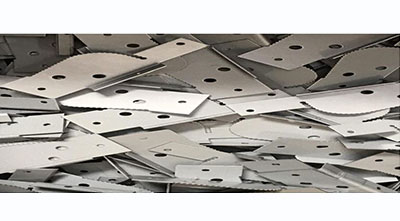
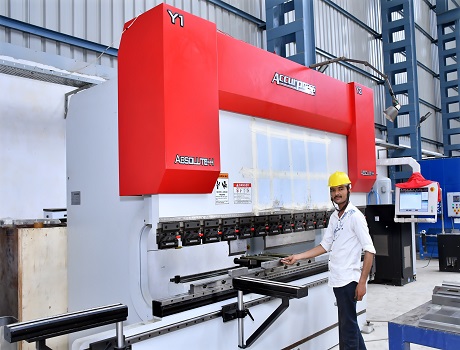
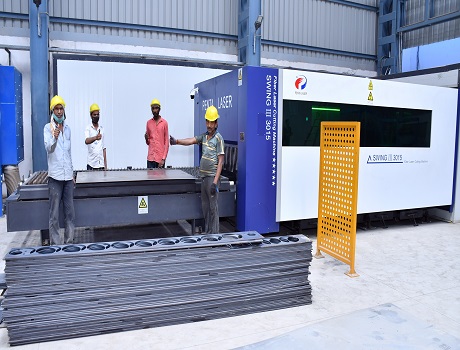
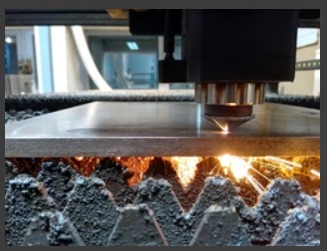
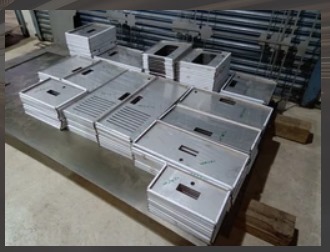
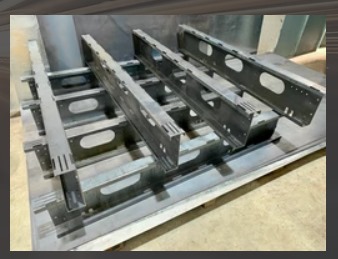
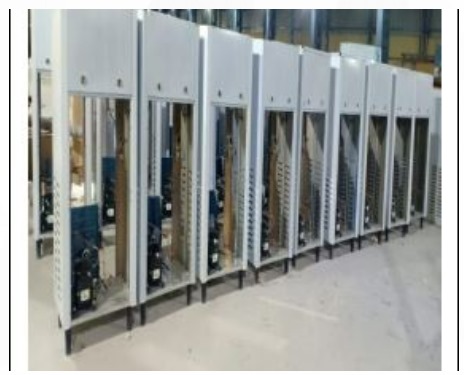
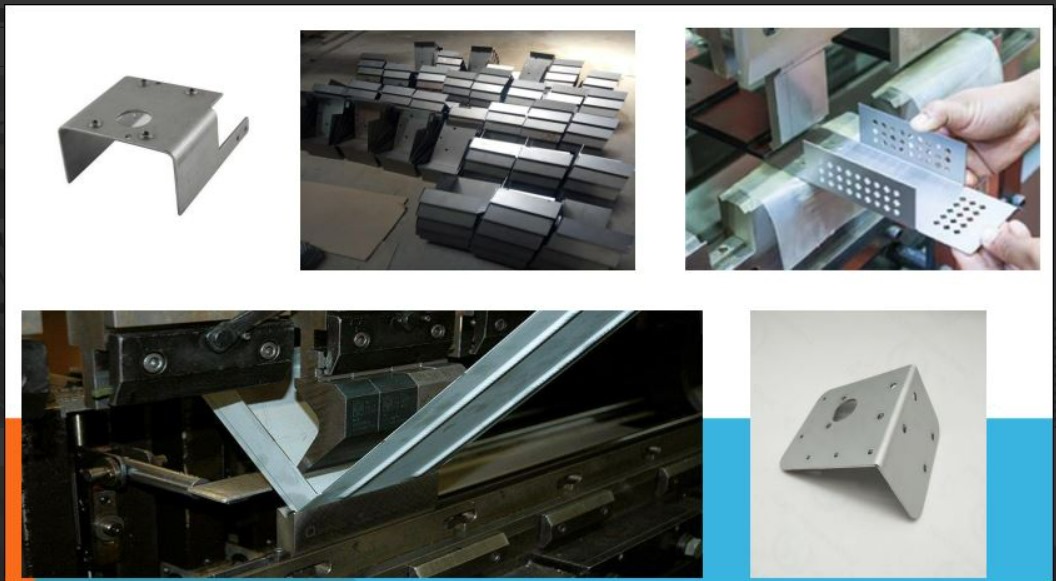
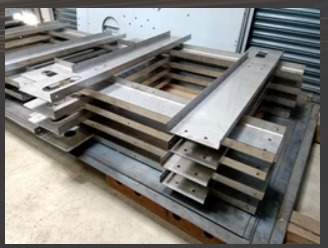